xplodee
Hot Rolled
- Joined
- Oct 14, 2013
- Location
- Allentown, PA
Hello All-
I have a production application where we need to impart a straight-grain finish onto 1024 aluminum after deburring. The logical choice would be a TimeSaver but the cost on those units is incredible! I'm looking into dual drum drum sanders like the grizzly linked below. I figured I could use 120g on the first drum followed by a ScotchBrite 7447 media on the second drum for deburring and finishing in one pass.
What I'm curious about is how well suited are wood-style drum sanders for metal finishing? Seems the SFM are pretty slow on them, so not sure why it would be a problem? Also, the Grizzly unit below states a 1/8" minimum board thickness but we would need it to go to around 0.0625" or so. Is this doable with a unit such as this? Is there a reason why people pursue a metal-specific machine beyond the added features (wet sanding) that those units facilitate?
www.grizzly.com
I have a production application where we need to impart a straight-grain finish onto 1024 aluminum after deburring. The logical choice would be a TimeSaver but the cost on those units is incredible! I'm looking into dual drum drum sanders like the grizzly linked below. I figured I could use 120g on the first drum followed by a ScotchBrite 7447 media on the second drum for deburring and finishing in one pass.
What I'm curious about is how well suited are wood-style drum sanders for metal finishing? Seems the SFM are pretty slow on them, so not sure why it would be a problem? Also, the Grizzly unit below states a 1/8" minimum board thickness but we would need it to go to around 0.0625" or so. Is this doable with a unit such as this? Is there a reason why people pursue a metal-specific machine beyond the added features (wet sanding) that those units facilitate?
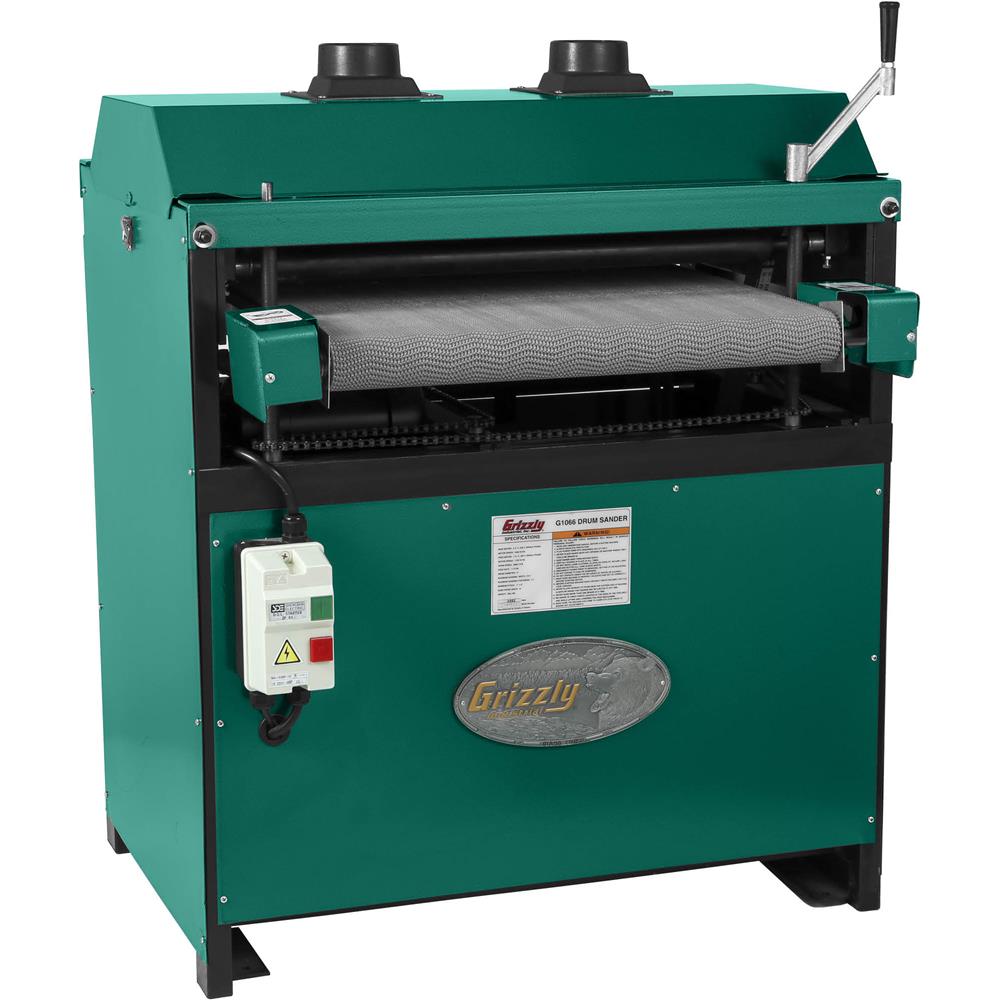
24" 5 HP Drum Sander
<h1>G1066R 24" 5 HP Drum Sander</h1> <h2>Offers dual drum sanding to cut your work in half.</h2> <p>This efficient drum sander removes planer knife marks and glue lines after panel glue ups with consistent board thickness.</p> <p>Minimize sanding time - the 6" dual drums allow coarse and fine...