Hi Folks -
I have been designing a combination lumber rack / chop saw station for my woodworking shop and have attached a couple of pics of the progress so far.
I'm planning to build it out of 2"x3"x3/16" box steel for the uprights, and 2"x2"x3/16" rectangular steel for the arms. Some welded flanges on the ends of the arms and then a bolt through the flange and upright with a pin affair taking the torsional load against the front face of the upright - picture shows the idea.
The majority of the weight will bear down on the concrete floor through the uprights, but it will be bolted up to the wall securly with lag bolts as shown.
There will be a chop-saw station on the bottom of the rack as shown, built over another row of arms.
I'm starting to wonder about getting all the arms exactly perpindicular to the uprights and if there is any way to design in some adjustment to the design. About the only way I can see to adjust the perpindicularness of the arms would be with small shim stock in between the pin and the front face of the upright.
Any comments or suggestions from someone that may have designed something like this in the past would be much appreciated.
Thanks !
Lewis
I have been designing a combination lumber rack / chop saw station for my woodworking shop and have attached a couple of pics of the progress so far.
I'm planning to build it out of 2"x3"x3/16" box steel for the uprights, and 2"x2"x3/16" rectangular steel for the arms. Some welded flanges on the ends of the arms and then a bolt through the flange and upright with a pin affair taking the torsional load against the front face of the upright - picture shows the idea.
The majority of the weight will bear down on the concrete floor through the uprights, but it will be bolted up to the wall securly with lag bolts as shown.
There will be a chop-saw station on the bottom of the rack as shown, built over another row of arms.
I'm starting to wonder about getting all the arms exactly perpindicular to the uprights and if there is any way to design in some adjustment to the design. About the only way I can see to adjust the perpindicularness of the arms would be with small shim stock in between the pin and the front face of the upright.
Any comments or suggestions from someone that may have designed something like this in the past would be much appreciated.
Thanks !
Lewis
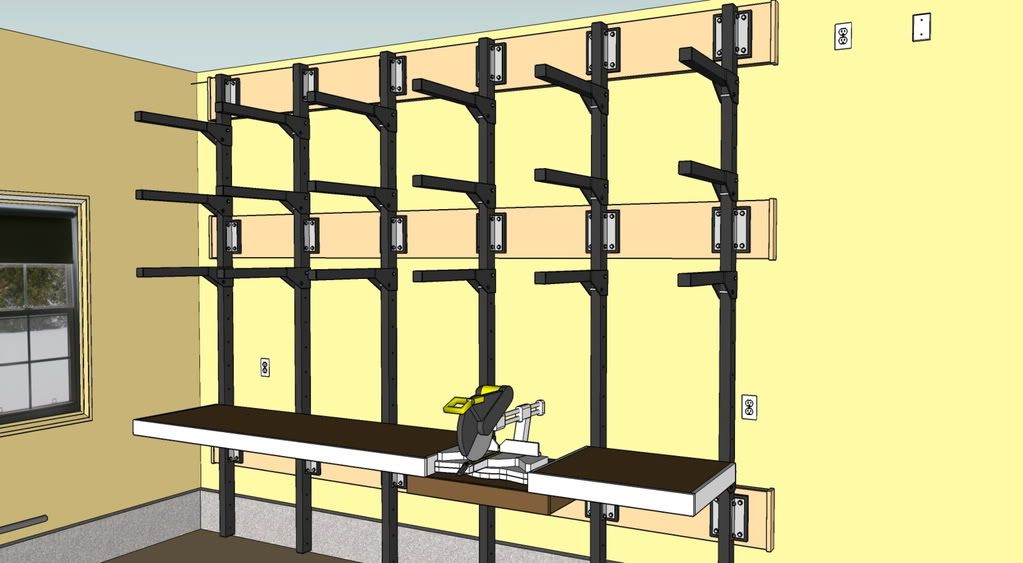
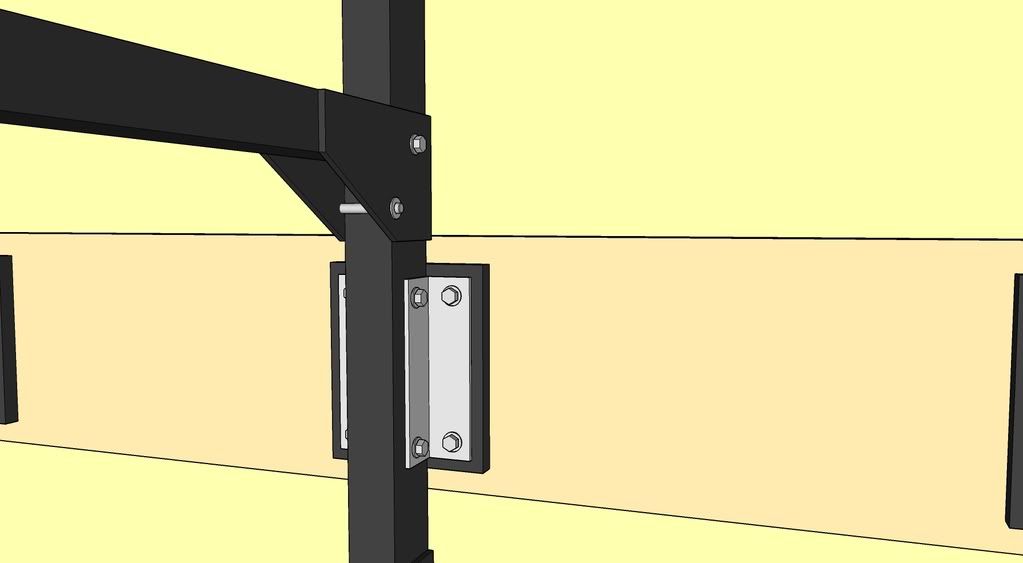