westcoastr
Plastic
- Joined
- Aug 6, 2021
- Location
- Bay Area
So I finally got around to pulling the side plate off of my mill head (Cincy 1-B Toolmaster) and look what I found in the “oil” system…enough grease to win WWII. Anyways…
Anyone know how to get the male friction hub and spiral gear circled in red off of the quill shaft? The book makes it seem like they just pull off, but there is nothing to grab on to and hammering the shaft to the right doesn’t seem a good idea.
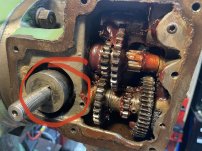
Anyone know how to get the male friction hub and spiral gear circled in red off of the quill shaft? The book makes it seem like they just pull off, but there is nothing to grab on to and hammering the shaft to the right doesn’t seem a good idea.
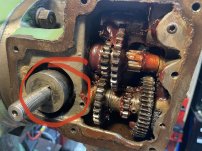